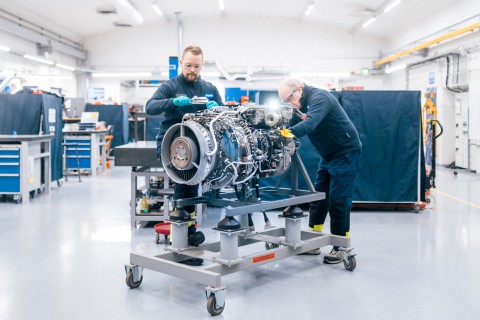
8.11.2019
When Aviation’s business model was revised in March 2018, it pretty much dropped a thesis topic into Mika Seppälä’s lap. Seppälä had been working at Patria for about ten years when, in autumn 2016, he began a degree programme in technological competence management at the Jyväskylä University of Applied Sciences alongside his work. In spring 2018, Seppälä was appointed as the expert in charge of item management at Patria, so it was natural for his master’s thesis to handle the same topic.
“Two things came together really well, as there was a need on both sides,” says Seppälä.
Easier to work with items
The thesis that he completed in May 2019 on item management and its development is no ordinary piece of work. Firstly, it was awarded the best possible grade. Secondly, according to the assessment criteria, it had significance not only for professionals but also for society as a whole. Thirdly, the supervisor praised the inventive and inspiring way the topic was handled.
And, maybe most essentially, the knowledge that Seppälä presents in his work has been adopted on a practical level in the Aviation Business Unit. Seppälä’s supervisor, Product Management Manager Mika Rasmus, says that Seppälä’s work has made daily life easier for him as a supervisor and for stakeholders as well.
In brief, Seppälä’s work is about how items form the cornerstone of a business’s ERP.It is mainly Patria’s own employees who have to deal with items, that is, the entire internal supply chain. If items are confusing or don’t really work, this creates a great deal of unnecessary work. Take, for example, a phone that has been assigned different item names in a system. Different people may search for it using the keywords phone, smartphone, cellphone, Apple or Android.
“And the search either will or won’t get a result,” says Rasmus, who commissioned Seppälä’s thesis.
The goal of Seppälä’s work was to create a self-contained service event that would also optimally benefit other organisations in item-related issues. The business unit has now set up a two-person team to focus on item management. Their task is to coordinate requests related to items, and also to ensure the accuracy and correctness of items – that is, quality assurance.
“For example, our centralised item management team will check whether a usable item name already exists to prevent too many overlapping item names from being created,” says Seppälä.
Now that item management services are available in one place, it is easy for individual employees or stakeholders to contact someone about item issues.
Based on lean management principles
The ideas in Seppälä’s thesis and the changes in Aviation’s business model reached far deeper into the organisational structures than the management of individual items alone. The changes in item management rely heavily on lean management principles, which in turn support the change in the business unit’s operating model. Everything starts with values and culture. Values define the principles that guide a company’s thought processes and decision-making.
Rasmus explains that you can’t put targets into practice if you are unable to influence a company’s prevailing working methods. He himself discussed and negotiated the changes in working culture, conditions and requirements that would have to be met in order for the operating model to be successfully changed. This generated an opportunity for a change in working culture.
Development work based on values and culture led to the adoption of the lean principle of flow efficiency. In practice, this means that the employee waits for the work rather than the work waiting for the employee. Seppälä says that, in accordance with lean principles, he first interviewed stakeholders who need to use items and asked them to explain what kinds of shortcomings they had encountered.
“I used the responses to put together a list of the most critical things that we needed to fix,” says Seppälä.
Concrete measures included compliance with FIFO (first in, first out) queue order principles, putting a ‘done in one go’ approach into practice, scheduling work, and introducing an item name creation form. Monitoring tools were naturally created for tracking the new service process. For example, it is now easy to visualise how many requests are directed at item names and how long it takes to handle these requests. Thanks to these process indicators, it is also much easier to predict the adequacy of HR resources.
Rasmus wants to emphasise that trying to introduce change solely through tools would have been a mistake.It was also vital to have an impact on culture, values and principles within the organisation.
“In his thesis, Mika has used lean management philosophy to demonstrate that you will not achieve anything permanent through the use of tools alone,” says Rasmus.
A transferrable model
In an economic sense, Seppalä’s thesis has benefited the business unit by reducing unnecessary work at several stages in the order-supply chain. His supervisor praised Seppälä’s thesis for its excellent practical grasp of the topic, and also because the methods it presented were not tied to Patria alone. In principle, an equivalent service process revision could be carried out at any other organisation working with an internal service.
Rasmus says that this process has now been productised at Patria, so the company is ready to provide training and implement the same service process revision on a turnkey basis in other parts of the organisation – and even for other companies.
Employer supports studies
In addition to its practical benefits, Seppälä’s thesis is a good example of combining modern working life and higher education studies. Seppälä is grateful to Patria for supporting his own initiative to study – for example, allowing him to participate in classroom teaching and to conduct interviews for his thesis during working hours.
Rasmus says that Seppälä’s thesis also excellently demonstrates how personnel training can be transformed into so-called “hard figures” when academic knowledge can be effectively adapted to practical work. One of Seppälä and Rasmus’s trusted colleagues said that the visualisation and monitoring of the new item management service model has “worked like a charm”.
“Mika completed a fantastic pedagogical learning path. As the person who commissioned this thesis, I can say that it hit the mark one hundred per cent,” says Rasmus.
And the development of centralised item management will definitely not stop here, but will continue with the aid of further measures. However, we have now created a firm base for the service process that can be scaled and further developed.
What did you like about the article?
Thank you for your opinion! You can share the article on social media using the buttons below: