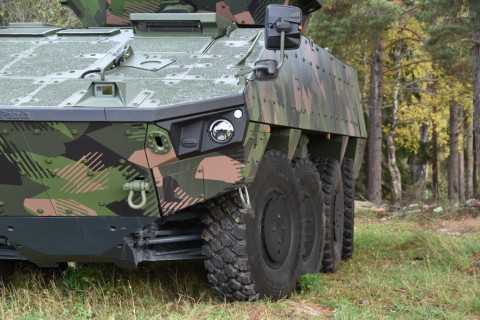
13.12.2021
Patria’s Aerostructures unit is a pioneer in the recycling of composites in the plastics industry. Responsible operations in these issues are an increasingly important competitive edge.
Text: Matti Remes
Plastic composites are used to make products such as boats, aircraft parts and wind turbine blades, but the recycling rate of composites is still low compared to many other materials.
The KiMuRa project is now seeking to improve this: in addition to Patria, the project involves six other Finnish companies that manufacture composites, the circular economy company Kuusakoski and the cement producer Finnsementti. Other industry sectors are represented in the project by the Finnish Marine Industries Federation Finnboat, the Finnish Wind Power Association, and Finnish Environmental Industries (YTP).
The project is coordinated by the Finnish Plastics Industries Federation, whose composites group is chaired by Mika Mustakangas from Patria’s Aerostructures unit. He says that the project has got off to a good start.
“We’re in the pilot phase, in which we’re already processing hundreds of tonnes of waste collected from companies.”
Utilising composite waste in cement production
KiMuRa comes from the Finnish words “kierrätetyksi ja murskatuksi raaka-aineeksi”, which means “turned into recycled and crushed raw material” – this aptly describes the approach developed in the project.
The companies involved in the project are developing their own approach to collecting waste so that composite waste can be collected and sorted separately. Via collection points in Kuusakoski, the waste is transported to the company’s Hyvinkää site for processing. The processed waste is delivered to Finnsementti, which uses it in cement production.
In the cement kiln, the fibre materials contained in plastic composites are utilised as raw materials with other cement ingredients during a parallel process, reducing the need for virgin raw materials. Plastic materials in turn are utilised as energy for heating the kiln.
“This process combines fibre recycling and plastics waste-to-energy. Most plastic composites are largely made of fibre materials, with a smaller percentage of plastic.
Effective recycling at Patria’s plant
Mustakangas says that Patria’s Aerostructures unit has created effective methods for sorting, collecting and transporting composite wastes in its production operations at Halli, Jämsä.
“The plant has collection containers for materials suitable for KiMuRa. Internal communications and providing guidelines to personnel are also vital so that they are aware of these issues and know how to do the right things.”
According to Mustakangas, cured machining waste is recyclable in this early phase of the project. It is currently being assessed how recycling will be extended to other composite materials, too.
“For successful recycling, it is essential that wastes are sorted correctly. This has been quite an easy phase for our skilled people.
Our established practices for recycling other waste materials are helpful. For several years now, the plant has sorted and delivered materials such as metals, plastics, paper, glass and timber to recycling and energy wastes for use in waste-to-energy generation.
“Our environmental expert Sari Jussila has been doing excellent work on this for a long time. She has also handled the practical arrangements of the KiMuRa project.”
An internationally advanced operating model
The KiMuRa project is part of the implementation of the national plastics roadmap and receives funding from the Ministry of the Environment. The project was started at the beginning of this year and its results will be announced in autumn 2022.
Mustakangas says that we can already claim that the Finnish operating model is advanced viewed in global scale as it enables the utilisation of various kinds of composite materials with extensive regional coverage.
“The key thing is that we have a very good team in which all the relevant subareas of this industry and topic are represented. They have worked together superbly to achieve our shared objectives. We’ve had great can-do good spirit.”
The project focuses on piloting a recycling solution for the production wastes of composite manufacturers. Mustakangas believes that in the future the solution can be extended to end-of-life (EOL) waste, that is, composite products that are being decommissioned. The project has already tested this successfully.
Material efficiency yields a competitive edge for Patria
Composite materials last for decades. Mustakangas considers it important to develop functional industrial-scale solutions for their end-of-life recycling as well.
“The Aerostructures unit wants to be among the pioneers in efficient materials utilisation in its industry – operating responsibly in line with sustainable development is an increasingly important competitive edge in these issues.”
Like other environmental issues, the possibility of recycling end-of-life products is important to an increasing number of customers in both civil aviation and the defence industry.
“Although plastic composites provide unbeatable characteristics in many new applications, they compete with other materials. For instance, metal recycling already has long traditions.
Civil aviation operators are now proactively looking for ways of reducing their carbon footprint. Mustakangas foresees that the environmental impacts of the defence industry will also be highlighted even more in the future.
“For this reason, Patria should look ahead and be among the first to take action so that we can offer products that are competitive in material efficiency as well.”
What did you like about the article?
Thank you for your opinion! You can share the article on social media using the buttons below: