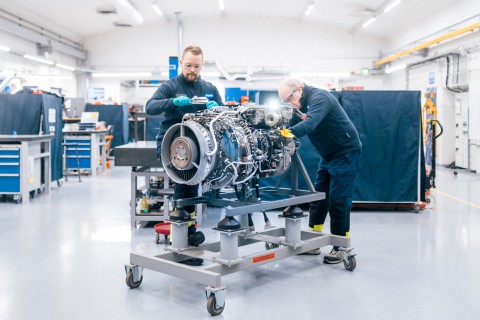
28.11.2018
Patria’s Aerostructures business unit is taking a big digital step by switching to paperless production and digitalized operations. An advanced stage of digitalization has also been reached in other internal processes.
Veli-Erkki Ruotsalainen is satisfied with the progress made in the project, which is nearing its end. “As a result of this project, all production processes will be performed electronically. We will finally be free of paperwork,” he says. During the project, which began in 2015, a dedicated factory network was built for Aerostructures, through which information is stored electronically and easily transferred from one computer to another. Investments have also been made in intelligent data management software solutions, implemented in a cost-effective manner by using Finnish sectoral expertise. “The benefits of a digitalised working environment are highlighted in a production project in which, say, 10,000 units of certain parts are produced each year. Under the old system, a pile of printouts was needed for each part and they had to methodically transferred from design through to production and archiving. Now, everything can be done with a few clicks,” says Ruotsalainen.
Information is seamlessly transferred from machines to people
Production is subject to obligations such as the collection of accurate measurement data and process results. Electronic documentation is a significant step forward in terms of the availability of data stored at different stages of production. Easily accessible data can be utilised more effectively in support of process management. "Looking to the future, we have a digital platform that will enable us to add new features. They may relate to the production of additional information for employees and the utilization of data from production machinery. For example, sensors may automatically monitor and record the temperature and humidity of the painting process,” ponders Ruotsalainen. The move away from paper manuals, and the use of electronic data processing, are key factors in production processes requiring precision, which help to reduce human error and increase the time available for work, particularly in planning processes. Ruotsalainen emphasises that employees will not save working time right away, because feeding data into a computer or tablet is no faster than traditional writing. Electronically available information and new possibilities for its use will be of much more fundamental benefit.
Computer algorithm checks and considers inventory levels
In addition to paperless production, Aerostructures has digitalized almost all office staff processes from invoice approval to work independent of place and time. In turn, computer algorithms have been harnessed for NDT machine inspections. Algorithms can check around five times more products than previous methods took in the same timespan. So this is about a huge efficiency gain. “The purpose of computer algorithm is to benefit from ERP. This is done by providing the algorithm with information on demand for the product and the desired inventory levels. It can create a precise production plan on the basis of these and other source data,” says Ruotsalainen. Digitalization has made rapid progress in technological terms. Despite this and the challenging situations they confronted, staff have approached the issue patiently. This change has impacted on almost all processes, and digitalisation has had some unexpected consequences. The accuracy of design data has improved to the extent that digital processes work as expected. In addition to harnessing the new technology, the key issue is to increase understanding of the transformation underway and to become better prepared to benefit from the digital environment. "Fostering staff competencies is at least as important as introducing new technology," explains Veli-Erkki Ruotsalainen.
What did you like about the article?
Thank you for your opinion! You can share the article on social media using the buttons below: